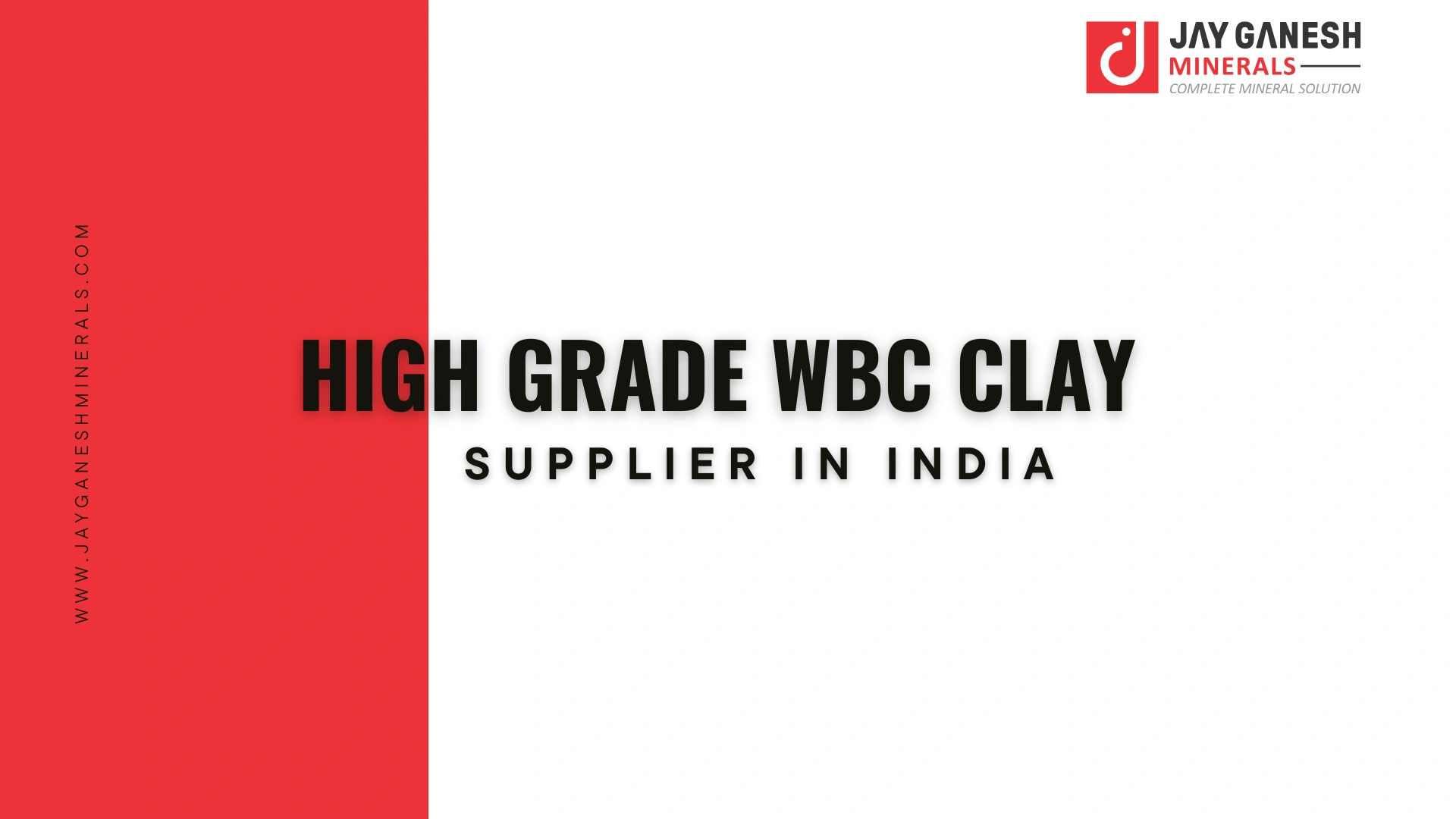
High Grade WBC Clay Supplier in India
10 August, 2025
07 May, 2025
In the field of ceramics and refractories (as well as jewelry), zircon and zirconium silicate are terms that are often used interchangeably. However, they are chemically related, but not the same thing. To understand the difference between zircon and zirconium silicate, industries such as manufacturing and gemology may find it beneficial.
Much of that confusion comes from their disparate elemental basis, zirconium, and their overall functions in those applications. However, they are quite different in their formation, purity, structure, and industrial importance. If you want to source materials for high-performance ceramics or pick a gem, you need to know which material you’re dealing with.
The chemical formula of ZrSiO₄ is a naturally occurring mineral and is known as zircon. Zirconium, silicon and oxygen make up the bulk of its chemical composition. It is formed in igneous rocks and is usually deposited in sedimentary deposits after being weathered away from its natural geological source. Some of the oldest minerals on Earth are zircon, some are over 4 billion years old.
On the Mohs scale, zircon is also known for being extremely hard (about 7.5) and corrosion and heat-resistant. The stone also has a high refractive index and strong dispersion, for which it is strongly brilliant. Natural zircon is, in fact, an affordable substitute for diamonds, especially in its clear and colorless form.
Key Properties of Zircon:
Chemical Formula: ZrSiO₄
Melting Point: ~2550°C
Mohs Hardness: ~7.5
High thermal shock resistance
Excellent chemical inertness
High refractive index (used in gems)
Beyond its aesthetic appeal, zircon has critical industrial uses. It’s used in high-performance ceramics, nuclear reactor linings, and as a foundry sand. It is also a key raw material for producing zirconium metal and zirconium-based compounds used in various high-tech applications.
It is a compound either extracted directly from zircon or formed through chemical processes, the result of zirconium silicate. Zirconium silicate will occur naturally as Zircon but is generally processed and treated differently if used in an industrial context. Zirconium silicate normally refers to the manufactured or treated ZrSiO₄ specifically for industrial use.
The difference in purity and particle size is the main point here. It is processed to remove impurities and to reach specific performance metrics of industrial-grade zirconium silicate. It is also used in ceramic glazes and refractories, and used as an opacifier in paints and coatings, etc. Zirconium Silicate is used abundantly in industries that demand durable and nonreactive materials due to its high resistance to heat, inertness to chemicals, and stability.
Key Properties of Zirconium Silicate:
Chemical Formula: ZrSiO₄
Appearance: Fine white or off-white powder
High chemical and thermal stability
Customizable particle size and high purity
Non-reactive with most chemicals
While the core chemical formula is the same as zircon, the difference comes from how it’s processed and applied. Zirconium silicate is not generally used as a gemstone and lacks the visual brilliance and clarity that natural zircon offers.
Zircon and zirconium silicate have the same chemical formula (ZrSiO₄) but different forms, purity, appearance, and usage. Zircon is a naturally occurring mineral that may be found as discrete crystals of gem quality. On the other hand, zirconium silicate is normally a processed or synthetic zircon introduced for a particular industrial need.
Zircon is a naturally occurring silicate of zirconium, while zirconium silicate is used by the industry after it has been refined from naturally occurring radioactive elements such as uranium and thorium. It therefore makes zirconium silicate more stable and safer for use in ceramics and coatings.
Zircon is transparent, translucent, or even opaque, and colors include blue, yellow, brown, and clear, in appearance. It is so brilliant and fiery that it is suitable for use in fine jewelry. The white or gray powder zirconium silicate does not exhibit any characteristic optical properties.
The hardness and density are also different. Zircon is denser and slightly harder in its crystal structure, also. Designed for consistent particle sizes in powder form to meet manufacturing requirements, zirconium silicate has reduced structural properties compared to its mineral counterpart.
Gem-quality Zircon tends to be significantly more expensive than it, but Zircon is also known to be somewhat more expensive overall. Thus, zirconium silicate is an industrially processed material that is both affordable and easily available in the market for its functional benefits rather than for its aesthetic value.
In different forms and under different demands, Zircon and Zirconium silicate present a very important role in different industrial sectors.
High-performance ceramic applications typically demand zircon due to its thermal stability and corrosion resistance. Casting molds for metals, nuclear reactor cladding, and the general manufacture of advanced refractories are all among the uses for it. It has the outstanding ability to withstand high temperatures and is thus able to survive extreme heat and pressure.
On the other hand, industries that need fine, nonreactive particles prefer Zirconium silicate. Ceramic tiles and sanitary ware use it as an opacifier; whiteness and opacity of glazes are the most common uses. The product is also used in the production of refractory materials, foundry sand, and even in paint formulations to increase durability and add resistance to wear.
A distinct and important difference between Design and Architectural services is that of cost efficiency. Bulk processing is easier and more affordable for the widespread industrial use of zirconium silicate. Especially in the higher grade forms, zircon is more specialized and much more often limited to niche applications or to the luxury market.
Zircon is a gemstone that may not be on every aficionado’s lips, but certainly not out of the world. One of the oldest known minerals on Earth, and is valued above all for its brilliance, clarity and the variety of its colors. Moved aside by synthetic rivals such as cubic zirconia, natural zircon is an appreciated, genuine gemstone.
That zircon is often mistaken for cubic zirconia is one of the most common mistaken ideas around. Although the names are similar, these are entirely different materials. Cubic zirconia is made up of diamond simulant and zircon is a natural mineral having optical properties like birefringence and fire that make it look deeper than cubic zirconia.
Blue, yellow, orange, brown, green and clear zircon can occur. The sky blue variety is commonly heat-treated to produce, and there is some variation in color hue and intensity, which can be attributed to the degree of heat treatment applied to both zircos and rubelfos. Zircon can also closely resemble diamonds in appearance, and generally, it’s one of the most underrated fine jewelry choices because even well-made, high-quality zircon can look superb.
Zircon is cut into many styles due to its relatively high refractive index and strong dispersion. Nevertheless, it falls closer to the middle on the hardness scale, which means it might need added care to avoid being scratched or chipped.
From the rough zirconite containing sand to the zircon or zirconium silicate, it goes through different stages of extraction, separation and refining.
Zircon is generally separated from other minerals by heavy mineral beach sand deposits using open pit or dredging methods. Often, there is also rutile and ilmenite within these sands, where the beneficiation processes are used to separate the zircon from the mix. Methods used for removing zircon from the raw material include gravity separation, magnetic separation and electrostatic separation.
Zircon that is once extracted can be used as it is in a natural state for industrial and gem applications or can undergo further purification. The mineral is also micronized to a fine powder for industrial use, especially when zirconium silicate is prepared. This means milling the zircon to decrease particle size, to be followed by calcination and chemical treatments to improve the purity and consistency of the zircon.
Zirconium silicate is a common product of mixed zircon purification with one or more flows of additional silicate input, particularly if it is destined for ceramics or refractories manufacture. Low levels of impurities such as iron and titanium are assured with advanced chemical techniques that can give them negative effects in high-temperature environments.
Modern developments have made processing more efficient as well as environmentally sound, with less waste and with still high material quality.
The decision whether or not to use zircon or zirconium silicate depends on your application and your need for performance. Natural zircon is the first material of choice when your focus is bulk ceramic tile production, refractory casting, or cast iron foundry applications because natural zircon is a cost-effective material and a very durable one. But if the product requires high whiteness, consistency in particle size, and purity, especially when this is for glazes or pigments, zirconium silicate is the preferred choice.
Jay Ganesh Minerals should work with a trusted mineral supplier who provides consistent quality in customized grades and technical support in order to achieve their production goals.
While zircon and zirconium silicate may look similar on paper, even sharing the same chemical formula, their real-world applications are quite different. Zircon, in its natural form, is rugged and versatile, making it ideal for high-temperature and structural applications. Zirconium silicate, being a refined version, offers superior consistency and brightness for decorative and functional coatings.
By understanding the differences between these materials, manufacturers can make smarter choices, reduce costs, and improve product performance.
Whatsapp Chatx
Hi! Click one of our representatives below to chat on WhatsApp or send us email to [email protected]
![]() |
Mr. RAJESH +91 99130 87000 |
![]() |
Mr. JIGNESH +91 89800 70055 |